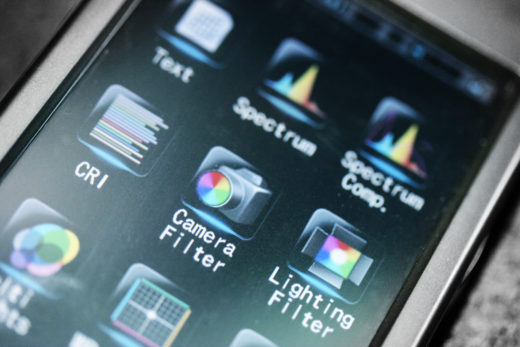
When Mole-Richardson launched its biggest, 3000-watt LED, there was much rejoicing – finally, a real LED movie light, with movie-light amounts of brightness. Three thousand watts was a lot for an LED then and it’s a lot now, although it costs as much as a car and is therefore only really capable of solving problems where power is really, really expensive.
Mole call it the 20K LED, which might sound like a rather incautious comparison; the efficiency offset with LED emitters and tungsten-halogen lightbulbs is often around four to one, whereas it’d need to be more like six and a half to one in a world where a 3K LED matched 20K of tungsten for output. Seductive as simple comparisons like that are, though, it’s not quite that simple, because we’re not comparing LED emitters and tungsten-halogen lightbulbs. We’re comparing the whole light, as it’d be carried onto set, and lights driven by tungsten lightbulbs are not built much like those driven by LEDs.
Brightness by geometry
A conventional fresnel, by almost any manufacturer, has three functional parts – a bulb, a reflector, and a lens. The bulb, tungsten or HMI, emits light into more or less a spherical area, give or take the socket on the bottom. Exactly how much of that is captured by the lens, or reflected by the reflector and then captured by the lens, depends on where you have the zoom control set – but it’s far from everything. Traditional tungsten-halogen fresnels give us lots of controllability, with variable beam angle and sharp shadow casting, but they’re very inefficient. A lot of the light – most, even – is firmly inserted into the walls of the lamphouse.
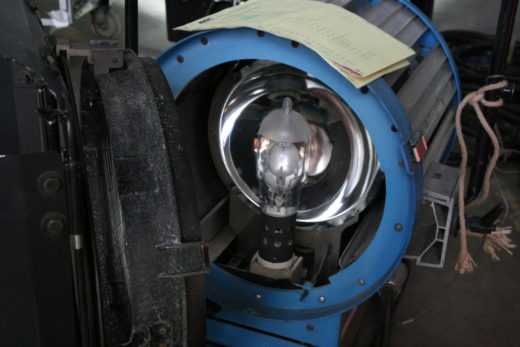
Compare LEDs. Let’s think about the LED equivalent of that conventional fresnel. The LED emitter array is essentially a circular object, with a reflector around it and the lens in front. Strictly speaking, there’s probably a layer behind the most fundamental light-emitting components that’s intended to reflect the light forward, but that’s part of the chip-on-board array, part of the lightbulb, not the light. Regardless, it’s pretty clear that the LED light’s layout captures far more of the light that the prime mover is generating. As a result, the LED fresnel can seem a lot more efficient than we’d expect because the LED facilitates more efficient lamphouse design.
Big diffusion, small efficiency
This isn’t even the most egregious example. Consider a large diffusion panel, illuminated from behind by a tungsten fresnel. It’s a tungsten-halogen lightbulb, which makes more heat than light. Then, the fresnel suffers all the inefficiencies we discussed above, even though we’re not using any of its focusing abilities. Then, we’re illuminating the back side of a sheet of (probably) some sort of white fabric, which is designed to be translucent but reflects at least some of the light. Then it’ll absorb some more of the light, before anything that makes it through gets to illuminate the set. This setup is woefully inefficient.
Compare a flexible LED panel like an Aladdin Fabric-Lite, which spreads LED emitters out on the surface of a textile to be rigged directly in a frame. Yes, the LEDs are four times the efficiency of the tungsten-halogen bulb but there’s no reflector, no lens, and no diffusion to reflect and absorb the light. This arrangement may be many, many times more efficient than a fresnel illuminating diffusion, with much more brightness, as well as taking up less space in the truck and studio and being faster to rig and move.
Double brightness, no electronics required
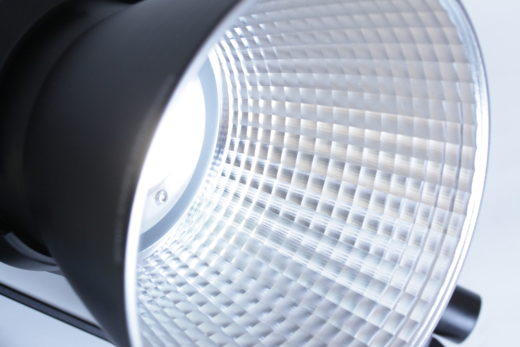
This stuff holds true all the way down to the smallest circa-hundred-watt options by companies like Aputure and Nanguang. Small LEDs around 100W sometimes come with Bowens-mount reflectors which make them functionally into a small PAR, although the reflectors are often a more sandblasted, dull finish than a true PAR. The closest historic equivalent is probably something like a Redhead, which was traditionally an 800-watt open-faced light beloved of news crews. It’s an efficient arrangement, with a reflector that surrounds the bulb more completely than the reflectors in most fresnels. Aputure deserves a mention here for realising its LEDs could get a lot better for a brighter reflector, and subsequently introduced a range of multifaceted types with highly polished aluminium reflecting surfaces.
The result was often most of a stop’s worth of brightness increase. A stop – not for any audacious piece of technological advancement in the LED emitter, but because of a better reflector, albeit with some credit for sacrificing beam angle to achieve that. This line of thought informs us about all kinds of interesting things, particularly the reason why larger-diameter fresnel attachments tend to yield a brighter beam from the same light – a larger diameter circle intercepts more of the light coming from the emitter.
With 1200-watt LEDs becoming affordable, it seems likely that people will keep making comparisons. Let’s be sure, though, to compare like with like – and accept that with LEDs behaving so differently to the things they typically replace, those comparisons inevitably involve things other than just comparing lightbulbs and LEDs.
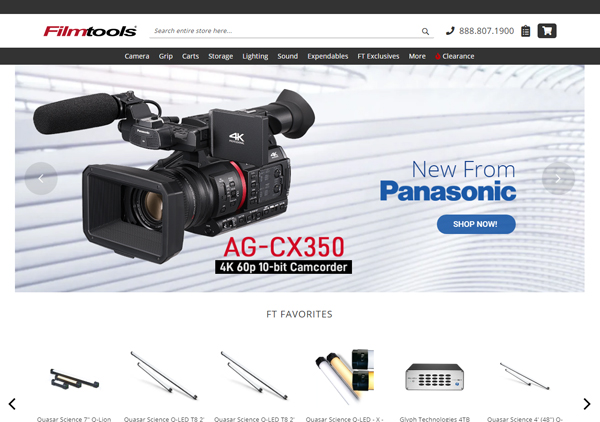
Filmtools
Filmmakers go-to destination for pre-production, production & post production equipment!
Shop Now